Machine vision systems in harsh environments
Ngày: 23/11/2020
How to protect cameras from environmental damage
Unfavorable operating environments are always a problem for a machine vision system when deployed in practice. This requires designers to have appropriate solutions to adapt or deal with in order to protect the machine system to be accurate, stable and durable.
Unfavorable environments can be very different, but in general, they are related to one or more conditions that hinder the operation, and can even damage the vision system. The most common phenomena are extreme temperatures, shock and vibration, exposure to dust, liquids such as water, etc.
.png)
For example, in food and beverage processing and packaging, vision systems are exposed to dust from flour, collisions from containers, sometimes explosions during filling, and liquids from routine cleaning and cleaning of food processing equipment. In woodworking, hazards include vibrations from equipment and machinery, and dust from sawdust. Weather warning systems operate in extreme weather conditions such as rain, extreme highs and lows. In outdoor inspection applications, cameras mounted on cars are exposed to weather and vibration, and some underwater applications are challenged by water and pressure.
In the past, the initial approach to harsh environments was to treat vision hardware as disposable and replace it when it no longer functions accurately within the allowable range. However, when using this approach, people often do not use high-performance components because their cost is higher. Therefore, using disposable vision hardware reduces the quality of the image.
Then, instead of using the above method, people will build custom enclosures to protect the hardware of the vision system, this technique is often used when the replacement cost of disposable hardware is high.
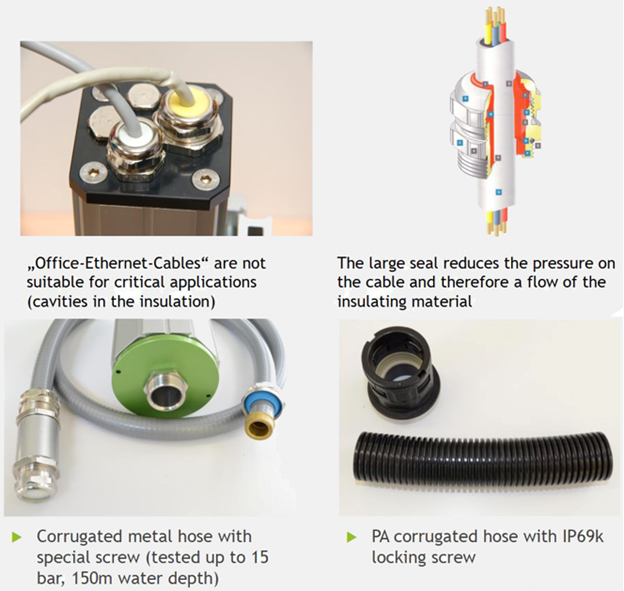
Temperature control
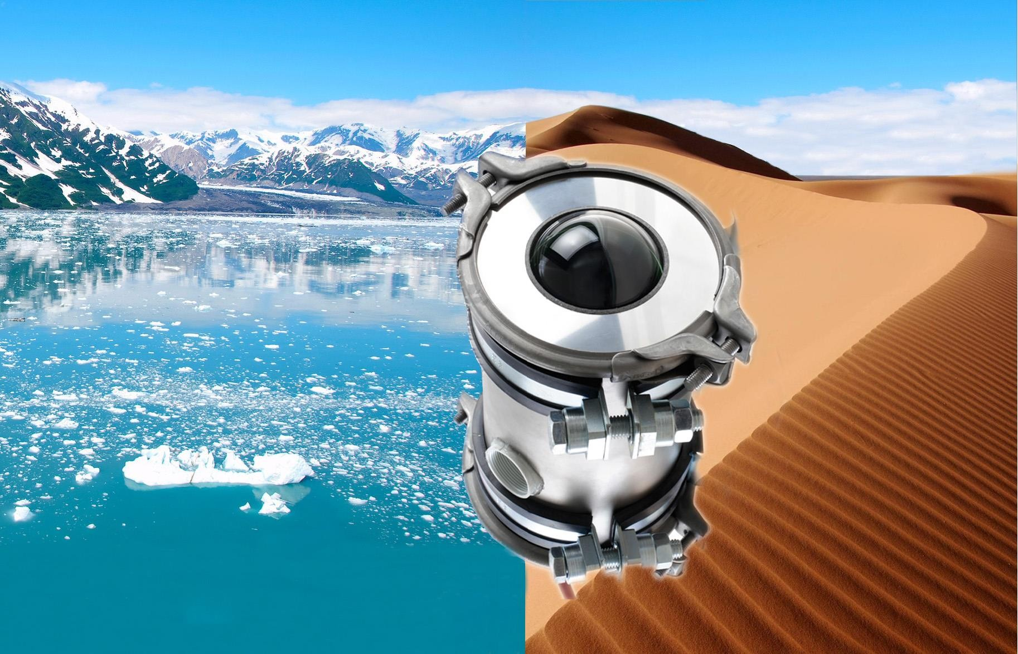
For most vision applications, the thermal challenges revolve around dissipating the heat generated within the device. Environments are rarely cold enough to impede device operation, but they are susceptible to overheating, which can cause device failure if heat dissipation is poor or ineffective. For best results, electronic devices, especially image sensors, should be kept below 50°C.
Traditional methods for temperature control include heat sinks and fans. High power applications involving lasers or installations in high temperature environments may even require water cooling. The specific choice is largely installation dependent.
Heat sinks are suitable for most applications, provided there is sufficient space, however they tend to be bulky and require free space around them for convection to occur. For image sensors, the heatsink itself can be designed to act as a heat sink.
Heatsinks are used in conjunction with fans to improve heat dissipation, or the fan alone can do the trick by circulating cool air through the system. However, to avoid dust contamination, the fan will need a supply of “clean” air, which is usually created by drawing air through a filter. Fans can be configured to draw air in, bringing cooler outside air into the case, or to exhaust air, removing hotter air from inside the case. In general, exhaust fans will wear faster, leading to premature failure.

In some cases, the system may have to operate in an ambient air environment that is too warm to dissipate heat adequately. In this case, the system may require alternative methods such as refrigeration or water cooling. Thermoelectric cooling of specific components such as processors or image sensors may also be used.
Vibration and shock
.JPG)
Vibration is a leading cause of a number of failures, including lens focus shifts, lens misreading from the camera, optical misalignment, electronics, and connection failures. Shock is also present in many installations - especially in machinery that engages in repetitive motion - and can cause similar effects. Both are mitigated using similar techniques, the most common of which are damping materials, additional locking screws, and thread locking adhesives.
Damping materials can be used in a number of ways. It can be placed at mounting points to reduce the transmission of shock and vibration from one piece of equipment to another. It can also be used in an enclosed space to limit the movement of units within that space. For focusing lenses, special damping greases are available to make the focusing motion stiffer and less likely to move.
Locking screws help prevent movement of optical system elements under the influence of shock and vibration. They can be particularly useful in systems with fixed focus or in systems that only need to be changed occasionally. Set screws with nylon heads can hold against shock and light vibration and have the advantage of not harming the focusing mechanism. In more severe conditions, conical or notched set screws will hold better but will affect the moving parts and will make the focusing movement rougher. Such set screws are best used with lenses that do not need to be refocused frequently.
Thread-locking adhesives help prevent screws and the like from loosening under vibration and can be used on almost all such locks. With lenses, there are few screws to lock in place, but there are retaining rings to hold the lens in the barrel. These rings can also use locking adhesive as long as care is taken not to let excess glue damage the lens.
.JPG)
Standards of some adhesives used
Water and dirt
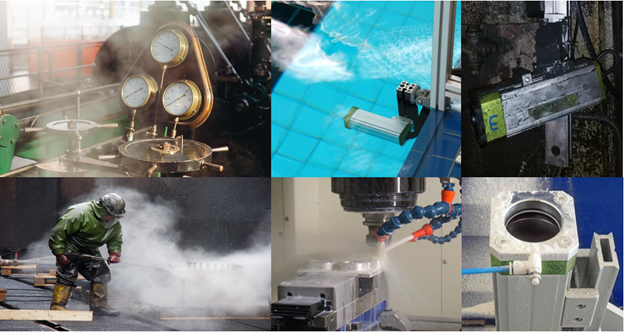
Some environments of steam, water, chemicals, dust in industry
Exposure to water or other liquids can wreak havoc on imaging systems by causing short circuits in electronics, resulting in equipment failure. Liquids can also damage lenses by damaging coatings or creating condensation that can reduce resolution and light transmission. Avoiding liquid damage depends on where the liquid is coming from. For accidental liquids such as rain, simply deflecting the liquid may be adequate protection. For immersion, pressure spray, or high humidity, watertight seals may be required.
The two main methods for providing watertight seals are adhesives and gaskets. Adhesives, such as room temperature cure adhesives and silicones, are relatively easy to apply and can be used in tight spaces, but can have issues with consistency and workmanship. They are also not suitable for joints that may need to be periodically dismantled, such as connecting a lens mount to a camera. In such situations, gaskets must be used, although they can be difficult to incorporate into small spaces.Gaskets are less variable in workmanship than adhesives. The most common form used in imaging systems is a silicone O-ring. Other materials may be used, but they must have very little water permeability if they are to be subjected to deep immersion or high humidity. Any moisture that gets between the lenses of the imaging system can cause fogging and reduced visibility throughout.
Exposure to particulate matter in the imaging system has the same effects as exposure to liquid: short circuits and obscuration of the optical path. Particle accumulation can also reduce the effectiveness of heat sinks and air cooling by adding a layer of insulation and, if applied with sufficient force, can abrade the external surfaces of the system.
Fortunately, the same methods used to prevent liquid ingress into the system will prevent dust particles.
However, one part of the imaging system that is difficult to protect from dust particles is the external surface of the lens. A flat optical barrier made of a suitable material may help provide abrasion resistance, but may do little to prevent material from adhering to the surface and obscuring the optical path. The answer in such situations is to periodically clean the external surface. This may require disassembly of the system to access the lens surface, thus adding to the cost of system maintenance.
A new option in lens construction allows the imaging system to be cleaned using a pressure spray system. Making an imaging system pressure cleanable is similar to making it waterproof with a robust seal. Providing a mechanical means to redirect the pressure spray away from the seal to avoid direct stress will help ensure a more robust seal.
The advantage of this option is that pressure sprays are commonly used to clean industrial equipment and facilities. The imaging system can be pressure cleaned, thus simplifying maintenance after installation. It is simply cleaned with a pressure wash at the same time as the rest of the equipment.
Pressure cleanable lenses are becoming commercially available, eliminating the need for imaging system designers to create their own solutions.
The International Protection (IP) standard (also known as Ingress Protection) classifies the degree of protection an assembly can provide against the intrusion of foreign objects or materials, such as solids and liquids. The IP rating format consists of the letters "IP" followed by two numbers and sometimes an optional letter. When no protection rating is available for a given criterion, an "X" serves as a placeholder. The first number, from 0 to 6, represents the degree of protection the assembly provides against the intrusion of solid particles. The second number, from 0 to 8, represents the level of protection the assembly provides against liquid ingress. The liquid ingress range has recently been expanded to nine to include ratings for high-pressure, high-temperature washdown applications. Achieving a nine rating requires testing with a pressurized nozzle at various angles.
.JPG)
Protection level IP EN 60529
While this approach significantly improves protection, it also increases the size of the vision system, making it impractical for space-constrained applications. Enclosures also tend to degrade optical performance because the added optical surface can distort the image, add unwanted reflections, introduce stray light, and cause other illumination problems. Furthermore, the added tooling also increases the cost of the custom housing system.
Neither solution is ideal, so camera and lens manufacturers are moving toward a third approach: developing machine vision components that can withstand harsh environments. This approach reduces maintenance costs and downtime by eliminating the need to constantly replace worn components or build custom housings.
Building an imaging system to survive in such harsh environments can be difficult. Each condition affects the system differently and requires the designer to use an approach appropriate to the specific environment. To address each environmental challenge, designers can choose from a number of standard techniques listed above.
With the advent of ultra-rugged imaging products, harsh environment imaging is finding new applications. Machine vision has been successfully deployed in food packaging inspection as well as in crop harvesters, industrial construction machinery such as dump trucks and cranes, consumer car guidance systems, unmanned robotic machines, marine biology equipment, and life science research.
For example, on a snack food processing line, a harsh environment imaging system is used in conjunction with a panel-level camera to detect whether packages are properly sealed, replacing manual inspection. When in operation, the camera sends an image of the package to a central processor that uses special algorithms to determine whether the package is sealed. The lens provides reliable visual detection of packages through a cloud of powder and other particles. Additionally, the system can withstand high-pressure washing at the end of each day to remove powder from the equipment. In a harvesting application, a camera/lens assembly mounted on a corn chopper sends images to an in-cab monitor, giving the farmer a clear view of the area around the 50-foot-long mower, helping him avoid hitting people or obstacles in the field. Using a machine vision system significantly improves safety and efficiency compared to the driver's visual observation. The harsh environment imaging system operates reliably in the dust, dirt, weather, and temperature extremes of the farm environment, and it survives high-pressure washing at the end of the day.
Harsh environment imaging has also found a home on construction equipment to give drivers a clear view of the area in front of the machine. These machines are often located high up, making it difficult for drivers to see people and objects directly in front of the vehicle. Machine vision systems send images to a display in the cab, helping drivers avoid accidents. The lens provides reliable images in the dusty environment of a construction site, and it can withstand heat, humidity, extreme weather, and high-pressure washdowns.
Key to all of these successful applications is designing the imaging system to withstand real-world conditions. By taking into account heat, vibration, water, and dust, designers are creating systems that can handle the worst that reality can throw at them.